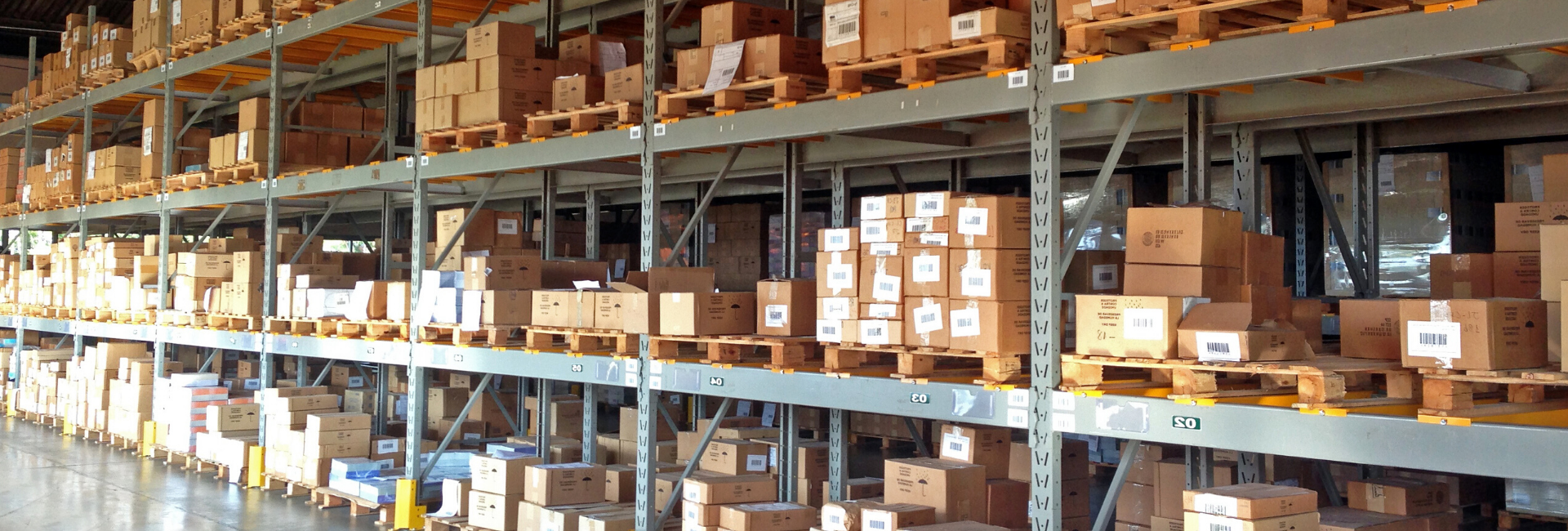
Soft and hard allocation: understanding the difference
Both are essential for efficient supply chain management
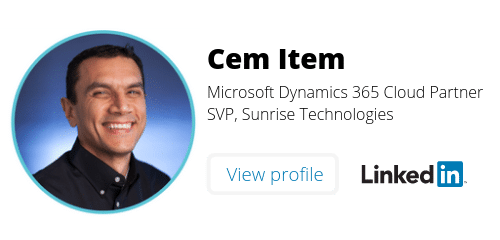
As the SVP of Global Business Development for Sunrise Technologies, Cem Item serves as a trusted advisor to C-level executives running large global enterprises. He conducts corporate business strategy engagements and digital transformation workshops around the world. With over 20 years of consulting experience, Cem specializes in the textile, apparel, footwear, home furnishings, consumer goods manufacturing, and retail industries.
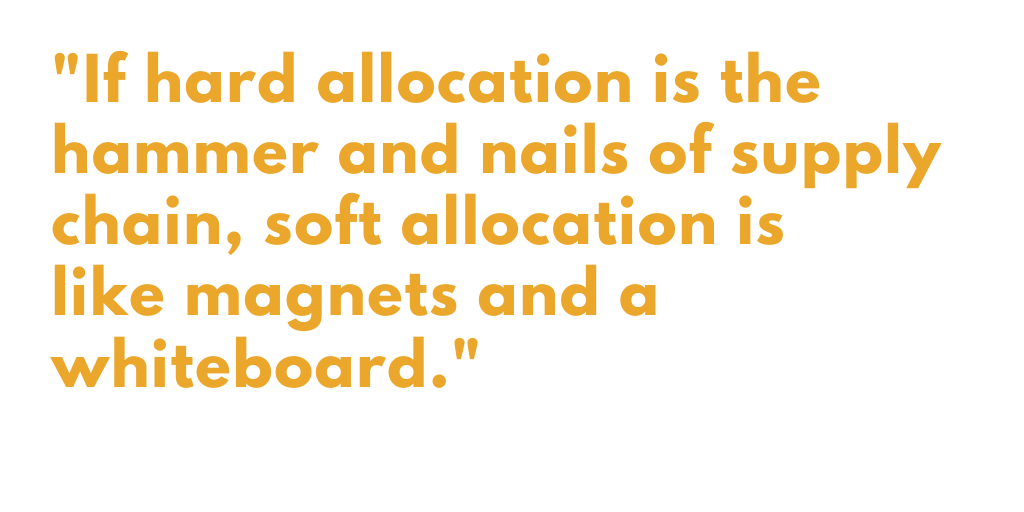
Defining soft and hard allocation
Allocation (the point where supply meets demand) is one of the most important pieces of the supply chain. So many critical business processes— customer service, inventory, sales — start hinge on smart allocation. Among supply chain professionals, software vendors, and other stakeholders, different words and terms get thrown around and people get confused. Here’s our point of view on hard and soft allocation, and challenges within each.
Very simply, hard allocation means the commitment between supply and demand cannot be changed. It’s been finalized, agreed upon, and now items are ready to go. Soft allocation, on the other hand, has a little wiggle room. Supply can shift as needed. Both practices play an important role in the supply chain, but typically we expect allocation to start out soft. Over time, as conditions change, allocation should get harder. During the planning process, hard and soft allocation can even be tied together.
Key differences between hard and soft allocation
Soft allocation
- Supply is flexible, depending on changes to demand. It’s possible to shift quantities and orders as needed.
- Usually, in the early stages of planning, soft allocation is the name of the game. Delivery is a long way off.
- Deals with planned and firm entities alike.
- More planning-oriented.
Hard allocation
- Supply is committed to the demand, with no changes.
- Delivery date is very soon…think days or weeks.
- Only interested in firm entities.
- More execution-oriented.
Challenges in the planning process
Planning usually starts with a forecast. Over time, orders are placed and users compare them to the forecast and adjust. The type of business can dictate how planning is handled. For example, wholesale businesses that gradually firm up demand over time may have semi-firm demand like a bulk or blanket sales order. For retail or eCommerce businesses, demand is never locked in until a customer places an order. Things get really complex for companies with multiple channels – retail, ecommerce, and wholesale, for example. Every channel requires different demand planning, from forecasting to bulk orders to placing actual orders.
Meanwhile, you also have planned purchase orders or production orders. Over time, these planned orders are scheduled, or goods are produced and delivered, and placed in inventory. All along the way, a company is juggling many types of supply (planned orders, in-progress orders, inventory, etc.) alongside many types of demand (the forecast, sales orders, standing bulk sales orders, etc.) And it’s the supply chain’s job to strike the delicate balance between the two.
How soft allocation helps you manage your supply chain
Let’s say you’ve just begun a new season, or otherwise in the beginning of the planning cycle. At this point, few orders are confirmed. You have a forecast, but products are still on order or in production, or something in between. This is the worst possible time to start hard allocating supply against the demand. You’ll encounter both inventory headaches from all the effort to re-organize and re-plan when orders are canceled or rescheduled, and you’ll have a bunch of customer service problems, too. This is the time when you should go with the flow. This is where soft allocation is your superstar.
If hard allocation is the hammer and nails of supply chain, soft allocation is like magnets and a whiteboard. While orders are being placed, you should be able to shift supply to demand as priorities change. Seeing the big picture — whether that’s by channel, customer, product, vendor, or other entities — is key to understanding and managing your supply chain for the best results.
Hard allocation comes into play when you’re ready to execute. At this point, you’re dealing with the firmest supply and demand (inventory and sales orders). Releasing the orders might be constrained by fulfillment rules, like no partial shipments, or at least fifty percent of line level is satisfied, or similar. Challenges at this stage are implementing these fulfillment rules while maximizing the amount of inventory that ships. The right allocation solution lets you set up and edit these constraints quickly and easily.