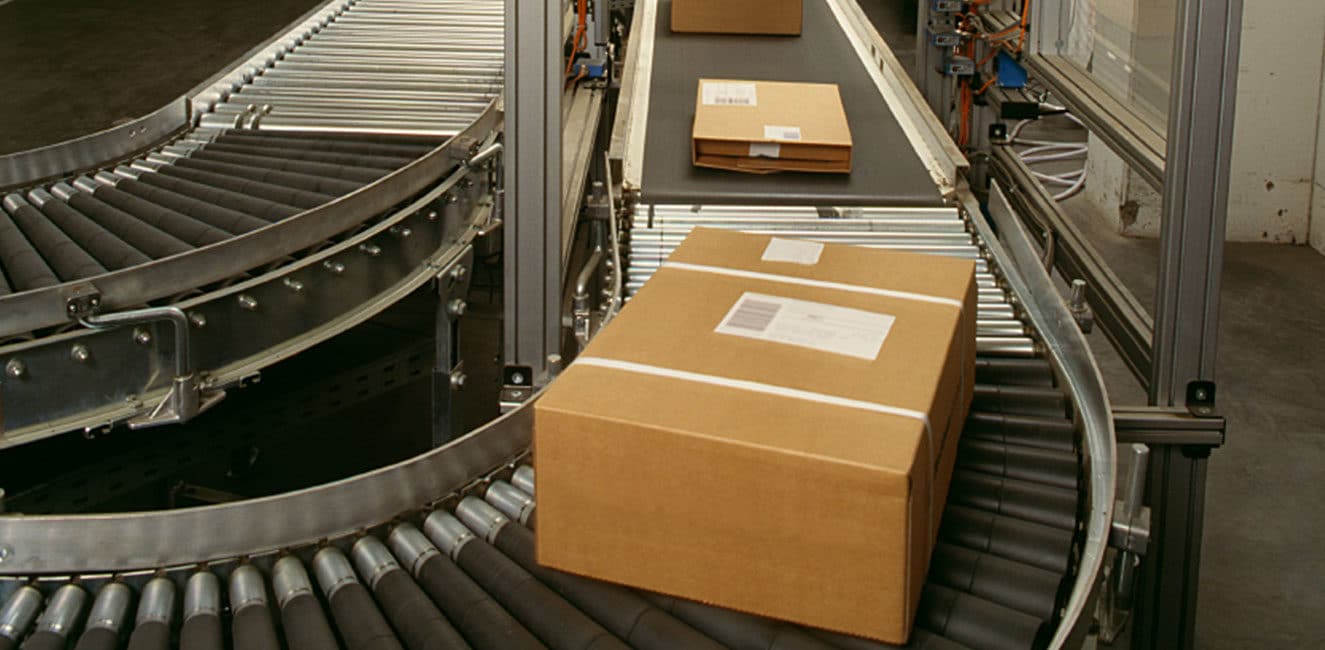
THE ROLE OF ERP
AND THE EVOLUTION OF THE MANUFACTURING SUPPLY CHAIN
Written by Mike Pereira, Vice President at Sunrise Technologies
The Role of ERP and the Evolution of the Manufacturing Supply Chain
Manufacturing supply chains have gone through a lot of changes over the years. Having worked with Apparel and Footwear manufacturers and Furniture manufacturers for nearly two decades, we’ve witnessed these changes and how manufacturers have especially been impacted due to increased globalization and consumer demands. While the market opportunities are enormous for manufacturers today, inevitably the environment in which they operate has become more complex. As a result, companies must be agile to be able to compete in this complex supply chain environment or be left behind.
Twenty years ago manufacturing companies executed most, if not all, of the supply chain parts and components by themselves using a vertical or centralized supply chain. The manufacturer would basically be in control of the entire supply chain process from stocking raw materials to distribution. Enterprise resource planning (ERP) software was still the go-to supply chain system for many larger companies and was adequate because most of the supply chain data was stored within a single enterprise.
There was a shift in the late 1990s when U.S. manufacturers began outsourcing their operations to lower-cost suppliers across the globe. This changed the way manufacturers manage their supply chains, adding much more complexity of decisions and data from various vendors and locations. Today, supply chains continue to grow in complexity and with fluctuating global conditions; manufacturers are forced to reconsider their supply chain strategies and the technology used to manage them.
Many of the furniture and apparel manufacturers we work with today were full vertical manufacturers. For instance, apparel manufacturers would have started from yarn, potentially owning the yarn manufacturing and continuing all the way up to a finished garment, finally distributing to a customer or wholesaler. For the furniture industry, you may have started from a raw wood substrate and fabric type that culminated into a finished product of a sofa. One company would manage all of the manufacturing steps that were attached to each of those subcomponents. So the company was purchasing all of the raw materials that it took to make that product and all of the subcomponents. Not that this was simple to model, but it certainly remained under one administration for management and decision making.
Today, that supply chain network has become segregated. The purchasing has become a more complex situation. You are buying sub components of your final product; you are buying fabric, cut parts, and maybe even just buying the finished good, and adding a final attribution to the product for your customer. You are the marketing entity, you are the selling entity, you are the merchandising entity, but you are most likely not manufacturing the product.
So from an ERP system perspective, how do you model that divided supply chain? A good example would be a production order. In a traditional sense, you created a production order for your own manufacturing facility. If there were five steps in the manufacturing facility, you simply had the subcomponents that matched the five steps in your supply chain; you went to step one, you made the subcomponent, you packaged that subcomponent, sent it to step two, and continued to the finished product.
When you get into the divided supply chain, you have to accept and depend on the vendor’s ability to produce that production order, including communication to that vendor as to what that production order needs to look like. Management becomes not only a planning issue within your company, but also a management issue, understand and have visibility of that subcomponent’s production in their facility and in the supply chain.
So our customers may ask, “Do I model the vendor’s capacity and the vendor’s execution of that production order? Because in the traditional sense, it was all mine, I managed it all, and I ran it though my system, but now it’s somebody else doing the work, it’s somebody else’s manufacturing location. How much control and how much visibility do I even get to what my vendor is doing?” They may have a vendor in China, a vendor in India, and/or a vendor in Mexico, in their planning process. They must consider which vendor is the most economical to work with on this particular product during a particular time of the year, and what is the capability of that vendor to even produce that product, even if they are the least expensive option? What is their capacity? What kind of relationship do they already have with the vendor? What kind of control do I have over this subcomponent? There are many different decisions that have to be made involving vendor control and the global aspect of those decisions toward the planning process to create a complete product.
We must have a system that will allow us to handle these challenges by modeling the supply chain in the relationships that I just described, being able to handle a production and purchasing arrangement between the company and their vendors. Microsoft Dynamics AX can model very nicely the finished SKU or finished good and all of the subcomponents of the finished good. We cannot only create our internal steps or production routing, but we can also create what is called a subcontractor work order or subcontractor relationship that resides within that supply chain network. For example, my process in the U.S. as a manufacturer is to screen print on an NBA jersey, but I purchase the blank jersey from someone in China. I have an exclusive relationship with that vendor in China, by which I can model their capacity and by which I can model a production order that is going through that vendor’s facility. The issue is that in order to invoke that relationship, I am actually purchasing a service from them, as well as purchasing the product itself. So you have to have the ability to have a purchase order and a production order so that you track the execution of the production but you can also execute the purchase from that vendor, and that’s the difference in the supply chain today.
Microsoft Dynamics AX allows you to engage with that vendor by modeling a work center at the vendor location; therefore, you can model the capacity, you can model a production work order going through that capacity, and you can purchase the service which is associated to that production. Transportation logistics can be modeled from a distribution perspective as well. You can model a warehouse location at that vendor and you can model the warehouse location at the back end of your supply chain, finally connecting them with a transportation operation between. This allows full visibility to when it is produced, when it leaves the vendor’s factory, when it’s on the water, when it arrives at the port, then arriving at your distribution center where you can complete your necessary activities of the supply chain process and distribute to the customer.
Microsoft Dynamics AX truly allows you to model that global sourcing supply network, and with the multi-site/multi-location capabilities of AX, you are able to model different countries in different ways for that product. Product with varying prices across countries, varying costs and BOMs, etc… but at the end of the day it is the same finished good item.
As manufacturers become more concerned about the need for technology that is capable of working across a network of trading partners, our customers look to Microsoft Dynamics AX as their go-to ERP software of choice which plays a vital role in centralizing transaction data and managing the global supply chain.
Let’s look at some ways Microsoft Dynamics AX can help meet these challenges for Consumer Packaged Goods manufacturers.
- Flexible Modeling to Meet Your Needs – Microsoft Dynamics AX offers flexibility through its unified models which provides a set of application concepts that reflect real-world business situations providing customers the flexibility to easily modify their organizational processes to meet their changing business needs. For instance, AX offers complete product modeling capabilities that can include the different variations of products being used within specific processes which helps prevent having to develop workarounds and invest in additional customizations to make the ERP fit in your product attributes.
- Increase Visibility – Visibility leads to your service capability. When your vendor can update the status of the work in process, you will know when you can service that due date for that sales order. An integrated ERP solution like Microsoft Dynamics AX provides access to critical real-time information about customers, suppliers, products, processes and the data needed to make informed decisions. Whether you need up-to-date inventory levels or to check production schedules, with Microsoft Dynamics AX you get the real-time information and insight into the supply chain that you need.
- Reduce and Control Costs – An inefficient and poorly managed supply chain can negatively impact every aspect of an organization, jeopardizing the performance of a company. With Microsoft Dynamics AX you can optimize your supply chain by centralizing data, standardizing processes, and gaining the visibility you need to optimize your business.
Manufacturers must embrace change if they want to make the improvements necessary to compete in this dynamic, increasingly complex industry. We’ve seen the companies which have successfully adapted and evolved their supply chain are now, not only the survivors in the industry, but have become the leaders in the market. While we are starting to see a shift that shows many companies’ manufacturing processes returning to the United States, and returning to a vertical manufacturing model, business will benefit from a system that is agile and powerful enough to work domestically and globally.